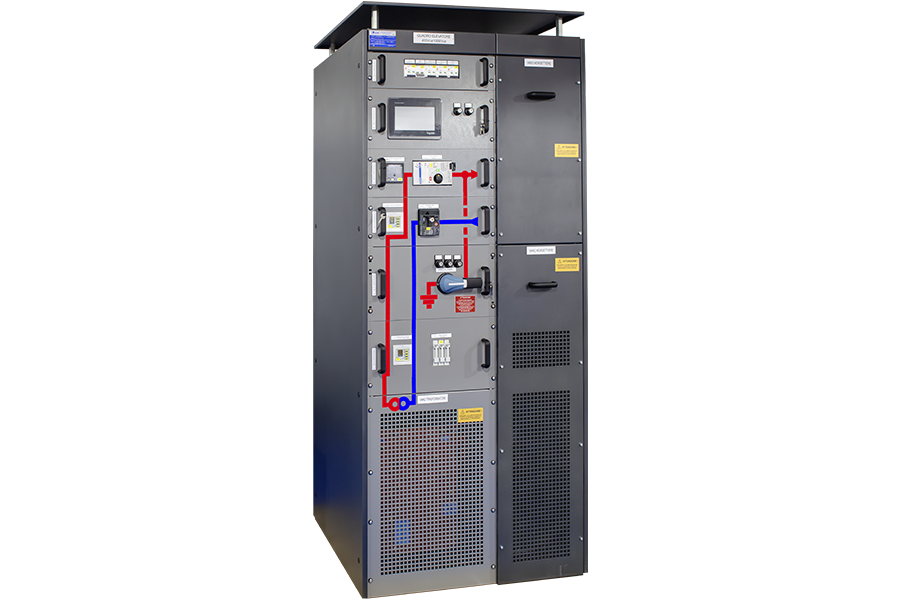
Electrical distribution panels to 1000 Vac for CCS systems
The Step-up switchboard is generally placed in the station and is powered by a no-break source such as an SIAP.
The purpose of such a switchboard is to raise the input voltage from 400Vac to 1000Vac with a transformer at IS365.
The aim is to obtain a power transmission line that has few losses and remains in low voltage LV with the resulting advantages in the use of components and associated costs.
The Step-down switchboard, on the other hand, is placed along the line and has the purpose of converting the 1000Vac line voltage into a voltage that can be used by 'standard' consumers typically 230Vac or 400Vac (single-phase or three-phase) or 150Vac.
This switchboard is essentially composed of a 1000Vac line input/output realised with two motorised isolating switches and a lowering transformer to IS365 specifications.
A section is therefore generally realised with two Step-up switchboard placed at the ends of the line and several Step-down switchboard placed along the line.
The automation of the switchboards is managed by PLC controllers suitable for working in outdoor environments as indicated in IS402.
In the Step-up switchboard there are touch screen monitors with the function of HMI to allow monitoring and management of the section locally, while in the Step-down switchboard there is a management PLC, but without HMI.
These switchboards are connected to each other via an Ethernet ring connection so that an interruption in the network cable (or fibre) does not affect functionality.
In turn, the Step-up switchboard have a dedicated Ethernet communication port for interfacing the system remotely if required.
Generally two servers are provided (for redundancy) to be installed in a central location or in any other place to be chosen by the customer to centralise data from one or more routes. It is then possible to create user workstations to operate on the route.
STEP-UP SWITCHBOARD
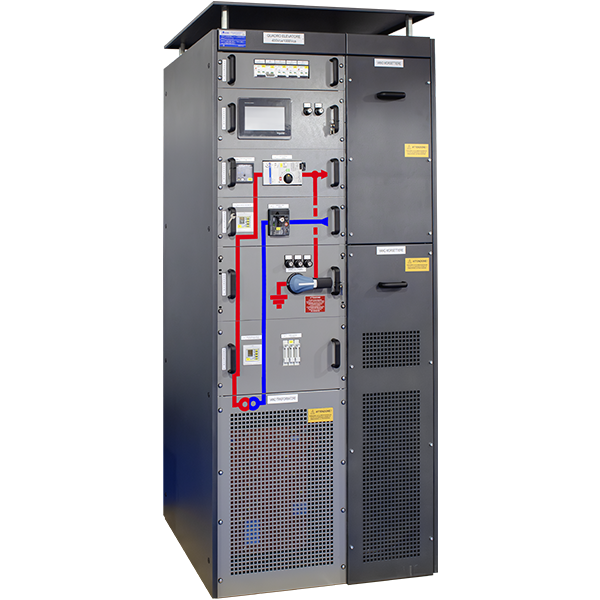
STEP-DOWN SWITCHBOARD
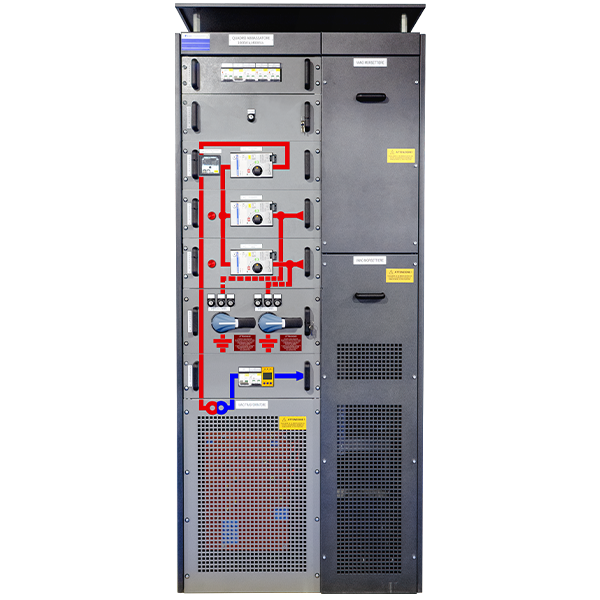
IP55 AISI 304 STAINLESS STEEL OUTDOOR - STEP-DOWN SWITCHBOARD
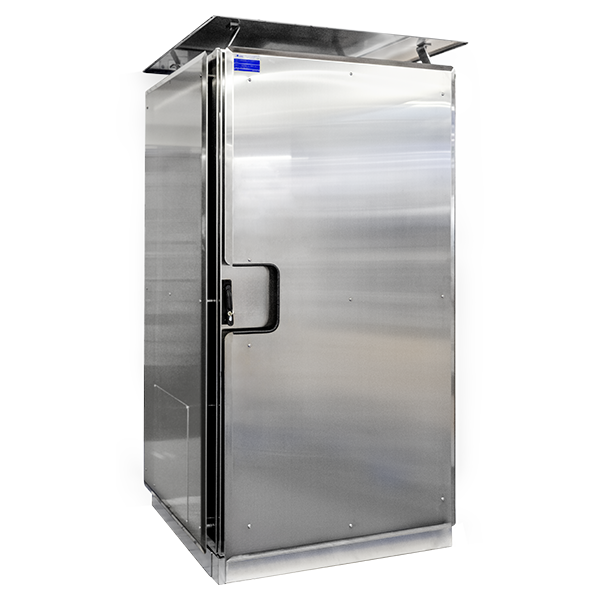
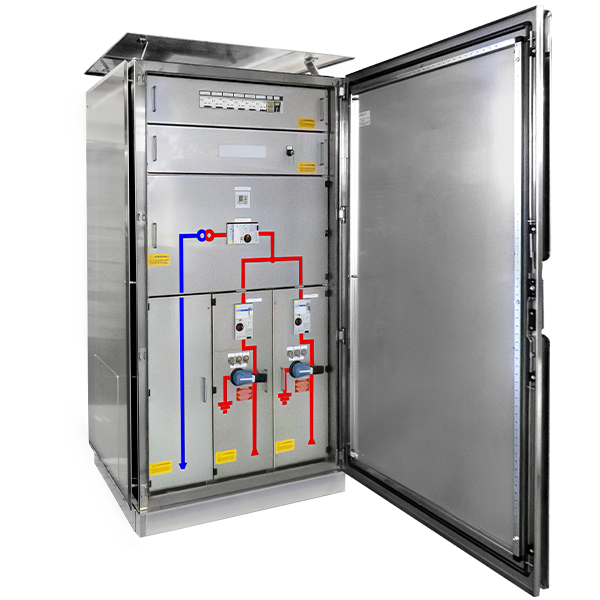
Related products
After Sales Services - CEG
Global Service Team
We provide continuous availability for any unforeseen event and prompt intervention for ordinary and extraordinary maintenance service both in Italy and worldwide.
Scheduled Maintenance
Maintenance works, customizable to the client’s needs, are carried out by highly qualified CEG employees.
Spare Parts
We guarantee and internally manage the complete availability of spare parts. Before delivery, all spare parts are tested and calibrated to match the specifications of the original components.
24/7 Telephone Assistance
A service designed for the immediate identification and potential resolution of faults, offering a reliable point of contact for clients who need a timely response.
Commissioning & Start-up
We check the correct installation of systems and ensure the main parameters are compliant under real operating conditions.
Training
We offer training courses that begin with theoretical sessions followed by practical ones, held at our headquarters, at the client's location, or directly at the site where the systems are installed.
Do you need a reliable partner to manage complex projects?
CEG Group operates as an EPC (Engineering, Procurement, Construction) Contractor. Thanks to its in-house engineering unit, CEG manages complete multi-specialist projects in the electrical and electromechanical fields. It provides integrated, custom-made solutions, ensuring its clients a full "turnkey" service that covers all project phases, from design to installation and commissioning, including maintenance.
The commitment of CEG Elettronica Industriale to quality is achieved through compliance with specific product certifications, compliance with international standards, quality certification, quality assessments, and external recognition.